
Printing a Better Future
By Matt Morgan
James DeMuth ’08 has pioneered a method of 3D printing that could change manufacturing forever.
When James DeMuth ’08 thinks about manufacturing 20 years from now, he sees an entirely different landscape.
Gone are bleak factories with lung-choking smog. No more complicated, wasteful supply chains. Instead, he sees a more open, innovative ecosystem: local facilities throughout the world using green technology to 3D print custom parts and components when and where they're needed.
The whole process is fast, logical, and clean. This is how you’d draw it up if you could start from scratch.
“Manufacturing must be closer to the customer,” DeMuth says. “Having products produced in a faraway factory has clearly failed to be the best economic and environmental approach.”
Sitting on the tail end of a global pandemic that wreaked havoc on manufacturing, DeMuth realizes this may all sound like a fantasy, but it's not to him. In fact, the first step toward a manufacturing ecosystem that offers a lower cost of entry, more opportunities for innovation, and less waste might already be underway.
Thanks to an innovation in laser patterning, DeMuth’s company, Seurat Technologies, is ready to build this ecosystem, and it starts with the 3D printing of metal. Through a process called powder bed fusion, Seurat’s latest prototype offers pixel-level design control while outpacing other 3D printers by 10 times.
“The goal is to transform manufacturing for our people and our planet,” the CEO and co-founder says. “We want to democratize manufacturing. You print parts where they’re needed, when they’re needed.”
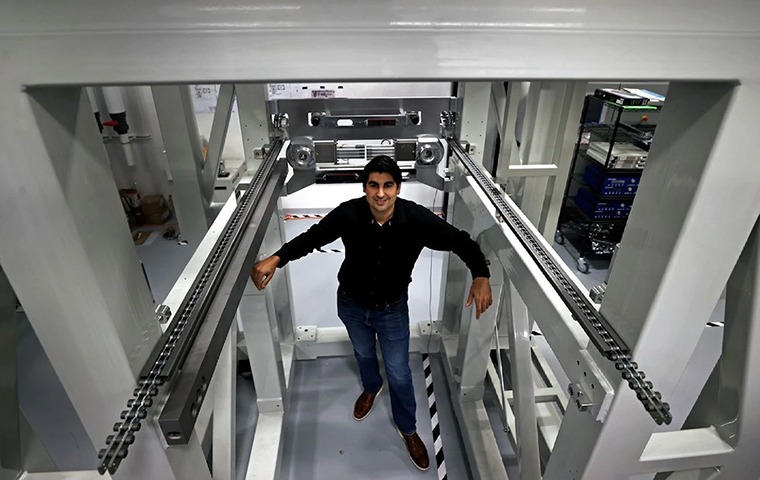
James DeMuth ’08 co-founded additive manufacturing company Seurat Technologies in 2015.
When people think of 3D printing, they’re usually picturing a process called fused deposition modeling, a hot glue gun style of printing popular with hobbyists. But 3D printing has actually been around in several forms since the 1980s, using lasers or UV lights to fuse resin or powder for highly detailed prototypes. Traditionally, these processes weren’t very efficient—only a handful of parts could be made at a time—but the cost and detail made them attractive for manufacturers.
Despite its shortcomings, 3D printing has long been considered a disruptor in manufacturing. Conventional methods like casting or forging are expensive, requiring manufacturers to create new tooling whenever they want to change a design. This high cost of entry limits innovation and boxes out eco-friendly methods which are desperately needed as manufacturing is currently one of the largest contributors to greenhouse gas emissions worldwide.
In recent years, 3D printing has shown promise in high-tech. SpaceX used a technique called selective laser sintering (SLS) to 3D print its SuperDraco rocket engine (and even a concrete building!). But when it came time to scale, the technology hasn’t kept up. In manufacturing, you need high production, good quality, and reasonable cost. Currently, 3D printing has been able to pull off one, maybe two at a time.
Seurat’s breakthrough in laser patterning could change that. Named after French Post-Impressionist artist Georges Seurat, who popularized a painting technique called Pointillism that uses small dots to form an image, Seurat has caught the attention of companies like Xerox Ventures, Siemens Energy, GM, and Porsche SE, securing more than $79 million in investments. Later this year, Seurat will open its pilot factory with its first production machine in Wilmington, Mass., with over 80 employees and more than 166 patent applications already to its name.
If DeMuth is right and Seurat’s new technology can make 3D printing more cost effective, that’s when everything changes—more efficient supply chains, fewer obstacles to innovation, and greener processes.
“We want to change the way the world does manufacturing,” DeMuth says.
Solving the right problem
DeMuth can track the beginnings of Seurat Technologies back to Professor Chris Kitts’ Robotics Systems Lab at Santa Clara. For his senior design project, DeMuth worked with Kitts to develop disaster recovery robots programmed to enter collapsed buildings after earthquakes.
The idea was to design small, four-legged robots equipped with wireless cameras and sensors that detect gasses like propane or natural gas. “They would essentially run ops inside disaster zones,” DeMuth recalls.
The project was ambitious. Robots with legs allow for more maneuverability—climbing over wreckage and other obstacles a wheeled robot can’t—but programming is far more difficult. With wheeled robots, you basically tell a robot to go, stop, or turn by slowing the speed of one side of wheels. For a legged robot, DeMuth had to program each limb to move individually and in concert with each other. Those commands were then correlated to a joystick so a user could drive it.
“We hadn’t done much with that. Most of what we were building was wheeled systems,” Kitts remembers. “But he was very talented and driven. He had a vision for what he wanted to achieve. I didn’t have to tell him to recruit a team with certain types of skills. He took care of all that.”
Within a few months, DeMuth’s robot could walk around the lab in Guadalupe Hall, and climb over obstacles several inches high. But even with their success, DeMuth couldn’t shake the feeling he was solving the wrong problem. While the robot worked, restrictions on battery life at the time—especially for the four-legged bot—were a serious problem. “You can only go so long on a battery pack,” DeMuth says.
In graduate school at Stanford University, DeMuth continued studying mechatronics and biomechanical design. But throughout his research, he, again, ran into the same battery issues over and over. “I decided I needed to solve the root of the problem,” DeMuth says. “So I went into the energy systems track.”
After graduate school, DeMuth went to work with the National Ignition Facility, part of the U.S. Department of Energy’s Lawrence Livermore National Laboratory. Among his first assignments was to design a large chamber used for nuclear fusion. Early on, DeMuth and his team tried powder bed fusion (PBF) as a possible solution. PBF is a form of 3D printing that spreads a thin layer of powder metal and uses a laser to melt—or weld—areas of the powder into a pattern. After one layer is complete, a spreader drops down to spread a uniform layer over the powder bed build platform area, more powder is added on top, and the process is repeated to sequentially bond each layer on top of each other, with the output built vertically, layer-by-layer.
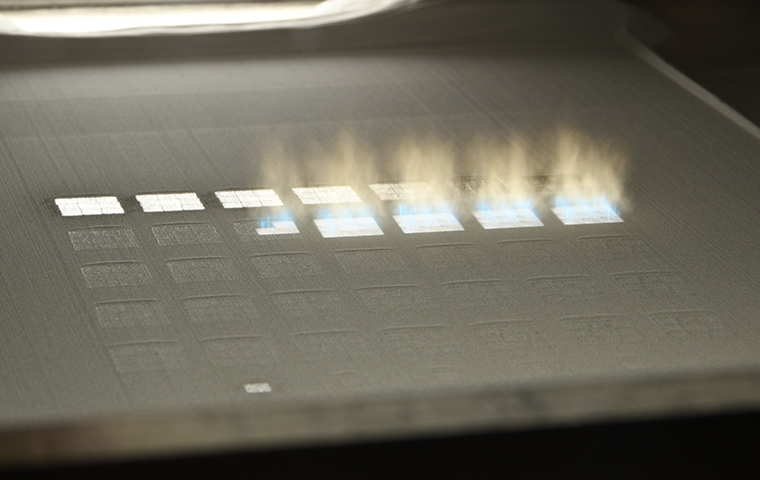
Powder Bed Fusion or Area Printing prints one tile next to the other. Over 2.3M pixels are used to define the shape of each tile.
While 3D printing offered the precision it needed, manufacturing a 39-foot nuclear fusion chamber with a laser the width of a hair was like painting the Sistine Chapel with a paintbrush with one bristle. “It was going to take me 200 years. That’s not going to fly,” DeMuth says. “Then we got into: how do we make additive manufacturing go faster?”
Going faster fundamentally requires more power, but doing that with a single laser greatly affects precision. Remember the Sistine Chapel? Try painting the eyes of Adam and Eve with a paint roller.
Another option is to run more lasers, but that is a delicate dance. Lasers in the powder bed have to avoid each other, which is possible but complicated. The bigger concern was heat and soot. With any kind of welding, the laser produces a soot cloud (like steam off a boiling pot) that lasers have to avoid and sparks that fly off when the powder gets too hot.
“They land in areas of virgin powder,” DeMuth says. “Since they’re irregularly sized, they don’t print the same as the other powder. They’re print defects waiting to happen.”
Finding the straight path
DeMuth says problem-solving was built into his education at Santa Clara. He didn’t just learn math or science skills he needed for engineering—he was challenged to look at problems differently.
In Professor Phil Kesten’s physics class, homework and tests often included estimation questions. Students had to estimate how many pizzas were consumed each week at Santa Clara. Or figure out how many ping pong balls could fit in a lecture hall. There were no right or wrong answers, just good and bad reasoning.
“It taught me to take a step back,” DeMuth says. “I found you could often find a straight path to get where you wanted to go.”
For DeMuth and his team at Lawrence Livermore Lab, they discovered a straight path in 2011 through laser patterning. You can think of DeMuth's process a bit like a zig-zagged funnel. At the top, a modular laser projects downward and is shaped into a square beam. That beam merges with a blue light pattern from a digital light processing projector. Farther down the funnel, a polarizing mirror splits out positive and negative polarization states before finally sending it to the powder bed for welding.
More simply, the process functions like camera film, dimming or letting through the parts of the laser it wants and eliminating the parts it doesn't. The result gives the printer the power of a big laser with the control of a small one.
“If I can choose my own power plant, then I can choose my own energy source. If I can choose my own energy source, I can guarantee I’m getting green, clean energy.”
“It’s as though you’ve split the one laser beam up into a million different individual pixel-sized lasers that are controllable,” DeMuth says. “But the image is continuous. There are no gaps in between the pixels. Each pixel can be on, off, or grayscale, and any value in between.”
With the discovery in hand, DeMuth took advantage of an agreement allowing employees to license inventions created at Livermore and go into business on their own. In 2015, DeMuth and his co-founder Erik Toomre, an operations veteran from Tesla, founded Seurat Technologies.
Seurat’s Generation 1 system produces a laser about the size of a postage stamp with 2.4 million fully controllable pixels. The powder bed and motion system can also handle up to 40 laser shots per second, allowing for the productivity needed to compete with traditional manufacturing methods.
Seurat’s advantage is additionally in temperature control. Because it’s a parallel process, the laser doesn’t have to move any faster or run any hotter than necessary, eliminating sparks and spatter, and greatly minimizing soot production.
On the cooling side, DeMuth and his team can offer highly customized parts by controlling the material properties of the output through crystal structure, grain orientation, residual stress buildup, and surface finish. With composition control down to layers of 25 microns (think heavy-duty aluminum foil), Seurat can produce components perfectly suited for complex, high-stress, high-fatigue, high-temperature environments used in turbomachinery and engine-related parts. DeMuth expects Seurat to initially print parts to be used in the consumer electronics, industrial, automotive, and energy sectors.
And unlike traditional manufacturing methods, as large OEMs release subsequent models to production, the design can be changed entirely with little investment in hardware. Companies wouldn't have to weigh the costs of new tooling, they just need to design it.
Dreaming of aircraft carriers and independent energy
The word disruptive is popular a lot in Silicon Valley, but in a space like manufacturing, it’s fairly easy to see the straight line between technological innovation and widespread impact. Seurat’s printer outproduces other state-of-the-art 3D printers by 10 times. DeMuth further expects each generation of Seurat’s area printer to outperform the previous by 10 times. “It’s an incredibly scalable technology,” DeMuth says.
How does that break down in the marketplace? Well, DeMuth expects Seurat to be able to produce highly customized parts at less than $25 a kilo by 2030. In comparison, silverware is about $35 a kilo, and metal screws you buy at the hardware store are $15.
“When you’re anywhere in that price range,” DeMuth says, “you’re talking about commodity items.”
By starting a new form of manufacturing that’s vertically integrated, Seurat is not only designing its own process but developing its own lasers and facilities and deciding where to put them. That means the company can shape an entire ecosystem that’s more efficient and sustainable, and possibly sheltered from global politics.
“The goal here,” he emphasizes, “is to bring back jobs to local communities, whether your local community is in the U.S. or Singapore. You have more flexibility to make the right business decisions.”
Vertical stage mirror used in the Seurat optical transport system
For instance, Seurat could build a factory near the original equipment manufacturers (OEMs) who buy them or set up factories near the metal mine where it procures its powder alloy. If they want to get real creative, DeMuth says, Seurat could potentially someday put manufacturing facilities on aircraft carrier-sized ships that sail from port to port. Parts would be printed onboard and unloaded directly to OEMs.
"There are lots of different scenarios you can dream up,” DeMuth says.
This flexibility could extend to power production as well. DeMuth can see a time when a plant would print 92,000 metric tons of metal components a year and use a third of a gigawatt of power. Rather than use an existing power plant, Seurat would build its own.
“If I can choose my own power plant, then I can choose my own energy source,” DeMuth says. “If I can choose my own energy source, I can guarantee I’m getting green, clean energy that’s not CO2 emitting—whether it’s wind, solar, geo, or nuclear.”
So far, Seurat has lived up to its promise. Remember that pilot factory, the company is building in Wilmington? It’s powered entirely by renewables. Seurat plans to follow a similar plan in its future locations.
“Energy is the engine of every economy, and we use a lot of it,” DeMuth says. “As new technologies and challenges force us to rethink how we power our world, we must transition to energy solutions that meet our nation’s security and economic needs and help us work toward our climate goals.”
Chief Scientist Andy Bayramian adjusts waveplate to complete optics upgrade on Seurat R&D system.