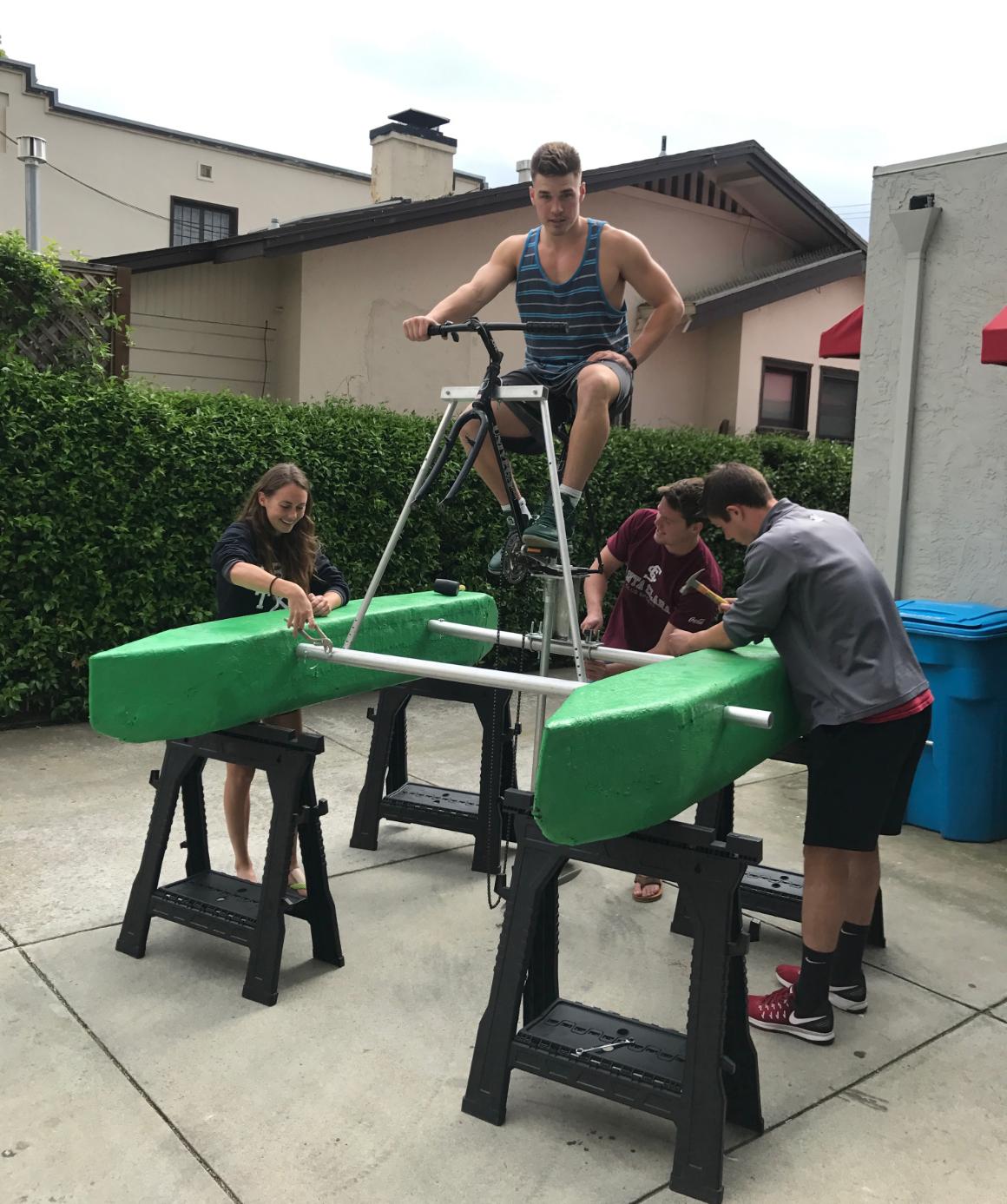
Fish Gotta Swim, Engineers Gotta Build
Heidi Williams
Designing, prototyping, and testing a human-powered watercraft using hydrofoils to reduce drag and send a craft speeding across a lake is no mean feat. It’s complicated, with seemingly endless interlocking details to consider and decisions to be made. This year, mechanical engineering seniors Sydney Lindeman, Joe McKenna, Conor Rounds, and Kyle Schumann took on the job of what their advisor, mechanical engineering chair and associate professor Drazen Fabris, says is “a very challenging project, in that they have limited power for the hydrofoil and need to be very efficient in their engineering. They are also required to engineer/design both stability and power, transmission, propulsion, lift, drag, buoyancy, and dynamics. So, as a project they need to do it all.” What would drive them to take on such a staggering task? Kyle has a simple answer: “We got into engineering because we wanted to build things. We wanted to make something we could actually ride, use, and enjoy.”
To build their craft, they mounted a portion of an upright bike frame on two pontoons made of polyurethane foam the team manufactured themselves, strengthening it with carbon fiber and fiberglass to prevent cracks or breakage. Two bike chains were joined together to give them enough length to twist 90 degrees. Conor explains: “The chain comes directly down from the first set of gears off the pedals, twists 90 degrees, and is hooked up to a sprocket connected to a driveshaft which turns the propeller.”
With a 4-foot-wide base and pontoons that are about 8 feet long, the watercraft would be stable in water, but the addition of two hydrofoils keeps it steady at a quicker clip. “In the back we’re using a dihedral hydrofoil with three wings to provide extra lift and stability in the roll direction, and one in front with a flat wing to provide stability back and forth and a little more lift and steering capability,” said Joe. Sydney notes that they had the hydrofoils cut “using an exact NACA profile, and we will coat them with carbon fiber, too.”
Initially splitting up into subsystem teams, they soon opted to do all the work together. “We found that all the systems are dependent upon one another,” Joe said. “You have to know how much power you’re going to be outputting to pick the right propeller. To do that, you have to know how fast you might be able to move. Until you draw that out, you can’t even design your hydrofoil, but you also have to factor in the weight of the boat and drag on the entire system, which affects how fast you can move. So this circular design process has been a little tricky."
Through it all, they are learning a ton, having some fun, and in the end they will have something they “can actually ride, use, and enjoy.”
Conor Rounds provides the pedal power as (from left) Sydney Lindeman, Joe McKenna, and Kyle Schumann adjust stability.