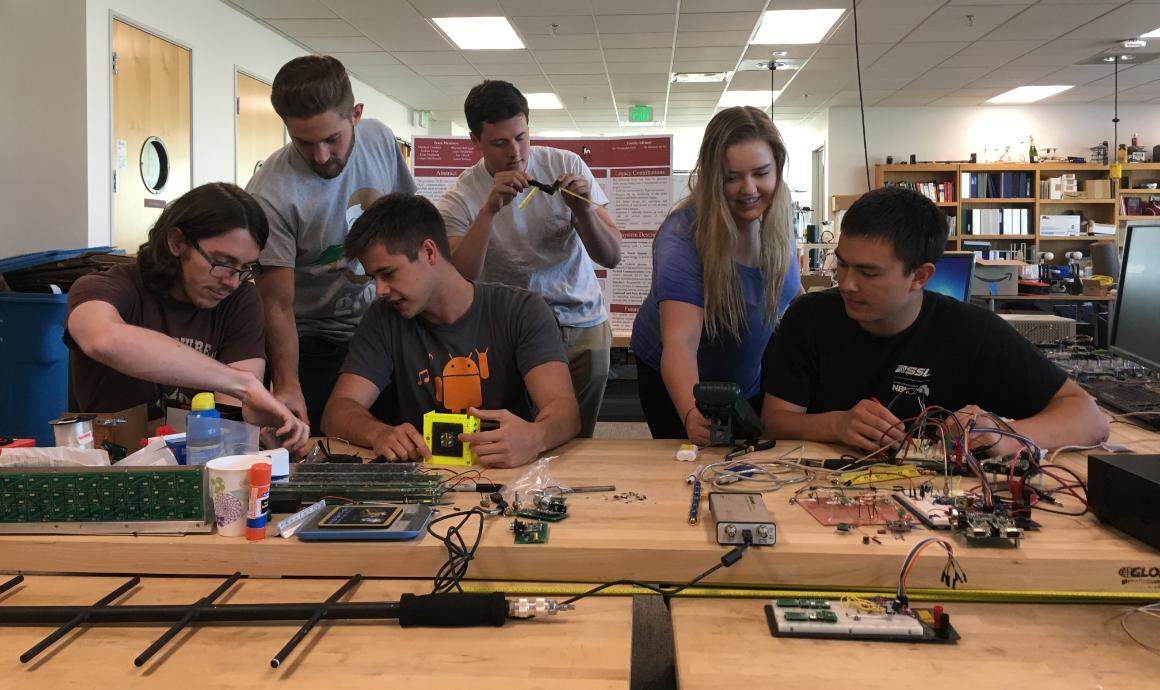
Interfacing Expertly
Heidi Williams
It’s fitting that a team of engineers working on a communications satellite would be good communicators, themselves. Yet in talking with members of an interdisciplinary senior design team (six mechanical and two computer science and engineering students) who are working on advancing small satellite technologies to enhance amateur radio disaster communications, you’d almost think you were meeting with a seasoned NASA crew.
Advisors Christopher Kitts, associate professor of mechanical engineering and director of SCU’s Robotics Systems Laboratory, and Michael Taylor, mechanical engineering assistant professor, are impressed with the team’s work across mechanical, electrical, and computing disciplines. “As a team,” Taylor said, “they are already operating with a level of professionalism very close to that which would be expected of them in industry as young engineers. They’ve internalized not only the technical aspects of our curriculum, but the organizational and system engineering aspects as well.”
Satellite Structure and Power System
In natural disasters, senior Matt Condino explains, people can’t rely on cell communications or traditional landlines that might go down. But a CubeSat satellite can use an amateur radio communications system to keep information about relief efforts flowing. “It’s easy to set up ad hoc networks and different nodes on the ground during emergency situations,” he says, “and our satellite will be able to send messages down to people and receive data messages from the afflicted area. That’s our mission and we have a lot of engineering that goes into achieving it.”
The entire narrow, foot-long structure is being machined in-house in the SCU Machine Shop, notes Isaac McQuillen: “It’s basically a little box that has two end plates, four side walls, and four rails that connect to the sidewalls. The rails have some tight specifications in regard to surface finish and size because they actually interface with the deployer. On the inside, we are using a few 3D-printed brackets to hold the circuit boards. In the future, 3D printing will probably play a much bigger role in these kinds of projects.”
“When a satellite is in space, the only way to generate any power is with solar panels,” said Andrew Drape. “All of the subsystems on the CubeSat run on 5 volt or 12 volt power. Previous senior projects designed a solar panel and circuitry to transfer power from the panel to regulated 5 and 12 volt lines. We’re taking both those subsystems and getting them to work together. We’ve also added circuitry to guarantee at least a one-hour wait time before any of the subsystems turn on after launch, per industry regulations, and we have a backup battery on board that can charge immediately and that will be used when the satellite is in eclipse from the sun.”
Gravity Gradient Boom and Attitude Control
The main radio antenna must face Earth; to achieve that without a lot of extra power or extra engineering, the team used what’s called the gravity gradient effect. “What that means,” said Brayton McKnight, “is that if an object is spread out in a certain direction, it tends to orient itself lengthwise toward the Earth as it orbits the planet. So we have a piece of tape measure coiled in the top of the satellite that we will deploy once we’re in orbit, extending and elongating the distribution of mass of the satellite to keep the antenna at one end pointed toward Earth.”
Cooper McDonnell explained further: “When the gravity gradient boom is deployed, it will either point in the right direction or be 180 degrees off. So we’ve put an Earth sensor on each end of the satellite. These sensors, or thermopiles, absorb Earth’s infrared radiation and determine if the satellite is in the right orientation. One end has the main data antenna which we will use to communicate with from our Mission Ops room here on campus. The thermopile tells us if we’re in position or not.”
Systems Engineering
“One of the main experiences we’ve gotten from a project of this scale,” said Laura Tschudy, “is a lot of practice with systems engineering—learning to coordinate what each team member is doing and what steps we should take, in what order. Some of that has been managed through the mechanical engineering department—we have our senior design class assignments to keep us on track—but we also lay out a lot of timelines and a lot of budgeting spreadsheets; not only for cost as you would normally expect, but we also have to budget for how much mass is going to be on the satellite, and how much power each component is going to be using. We’ve set up a lot of those types of documents to manage information along the way.”
Summing up the team’s experience, Isaac drew knowing laughter from his teammates when he said, “One of the biggest challenges of this project has been controlling the interfaces between all the different subsystems on the satellite—the power system, computer boards…. Anything that goes in the satellite is subject to a lot of change—we’ve seen that throughout the project! Keeping track of how a change in one area affects everything else in the satellite was a challenge for us to wrap our heads around a couple of times.”
(From left) Matthew Condino, Andrew Drape, Brayton McKnight, Isaac McQuillen, Laura Tschudy, and Cooper McDonnell at work in the Robotics Systems Laboratory. Photo: Heidi Williams