Something that becomes abundantly clear as you progress through the senior design project is that an idea “on paper” often does not fully translate physically in the prototyping phase. Because at this point in the senior design project your team should have an ideal vision of what your design solution will look like, it is likely that component fabrication, debugging, stress analysis, and assembly may bring about issues that demand further design iteration. And, in most cases, these will be issues that you and your team have not yet discussed or dimensioned for in your previous design meetings. Coupled with the need to verify your prototype or conceptual design model with tests and data analysis, time will often be at odds with the goals of your team.
The senior design project limits your team in time and resources. One thing will become clear in the project because of this: you and your team may not be able to address all of the problems with your design before the end of senior design. As a result, these constraints bring about the need for teams to consider what trade-offs need to be made in order to have the best representation of their design solution prepared for faculty and professional engineer assessment at the Senior Design Conference. Because of this, your team may need to revisit aspects of the design, enumerate existing problems, and discuss which of these problems may be addressed with the time and remaining funds at hand.
Utilitarian considerations ensure that you will address the right problems and minimize the number of issues with the safety and functionality of the design. Problems that demanded that my team and I consider the trade-offs in our conceptual design included:
Lead Time, Cost, & Quality of Implemented Solutions:
As design iteration can happen anywhere in the design process, there may be changes in the design that demand the re-fabrication or purchase of new parts, materials, or configurations that are inconveniently close to a deadline. This was especially true in my own senior design project, in which I worked within a team of four mechanical engineering students to design a manual clay brick press for a social entrepreneurship in Nicaragua. I witnessed this at all phases of our prototype fabrication phase-- even well into the week before the Senior Design Conference. Prototype problems that appeared closer to the conference brought our team to realize that it was impossible to devote the same level of time and detail in redesign and re-fabrication of parts and still complete our prototype on time. Similarly, there were problems that would have been best solved by purchasing additional materials, however, our team simply did not have the time nor dispensable funds to wait for those materials to arrive. To help our team decide the best course of action in the completion of our prototype we would apply a Utilitarian Approach in design thinking to address three main variables: lead time, materials cost, and quality of the solution.
What was important for us to consider was that all three variables had to be considered in order for our design change to agree with the resilience of our project and our standards as engineers. While one variable would sometime seem more important to address than the other, a combination of minimizing lead time and cost while ensuring the highest quality solution we could produce was the goal of each design change that we made in the prototyping phase.
Lead Time: This is the time taken for your part or parts to be ready for assembly, whether it be through fabrication in-house, employing professionals, or through shipment from an external vendor.
When considering how lead time factors into Utilitarian considerations in decision making:
- Would an increased lead time on a part result in a higher quality design solution? Similarly, would a decreased lead time result in a less quality solution?
- Would an increased lead time on a part halt the progress of other critical aspects of the project?
- What would a decreased lead time on a part cost your team? Is this an affordable expense?
- Suppose your team did have the time to make design changes. What design changes would you implement to improve the safety and effectiveness of your design? Can any of these changes be implemented partially or fully before the Senior Design Conference?
Materials Cost & Fabrication Expenses: This is the dimension of how team resources are depleted by making design decisions. While this could be understood in terms of funds, this also includes the depletion of your team’s stock of building materials.
When considering how materials cost and fabrication expenses factor into Utilitarian considerations in decision making:
- Would expending more team funds maximize the quality of the part to be fabricated/purchased? Is this within the team’s budget?
- It is possible that your team will look to minimize project costs by using cheaper materials. Can these cheaper materials be used while still minimizing the chances of compromising the safety or effectiveness of your design solution?
- One thing your team may also run into during assembly is that you may need to redesign a component or subsystem. Does your team have the stock of building materials necessary to implement a design change? If not, how would this impact the safety or effectiveness of the design solution?
- Suppose your team did have the money to afford the purchase of newer and better materials. What design changes would you implement to improve the safety and effectiveness of your design? Can any of these changes be implemented partially or fully before the Senior Design Conference?
Quality of solution: This describes to what extent the design decision that is made solves the problem at hand. Design against failure, wear/rust resistance, weight, efficiency, lag time, precision, sensitivity, and even aesthetic features all contribute to the quality of the prototype.
When considering how the quality of the proposed solution to a design issue factors Utilitarian considerations in decision making:
- Your team may find a higher quality part or design solution to implement for your design, or find the need to send out parts for professional fabrication. Is there room for this lead time in your project schedule?
- Would a higher quality part or design solution be within the team’s budget?
- Additionally, there may exist higher quality solutions that are not within your budget. If a higher quality solution cannot be afforded or there is not enough time to implement it, would it compromise the safety or effectiveness of your design solution?
- Suppose your team came up with a much better solution to a design issue very close to the Senior Design Conference, but had a lesser quality solution that “works”. Would the benefit of investing in this supposedly better solution be greater than the cost of possibly missing a deadline?
Personal Link:
Three weeks before the Senior Design Conference, my design team and I learned of a critical design failure in the Compound Lever Arm subsystem of our clay press. Because we used a hollow square tube instead of a heavier and more expensive solid rectangular member for this system, we could not drill holes through the beam and bolt other pieces onto the beam.
Two options arose in our team meetings, which we discussed at length with our faculty advisor and tested in Solidworks and Abaqus. To use a beam with a larger wall thickness or use a solid rectangular beam would have allowed our design to remain the same, but would have increased the cost of the subsystem by $40-- a non-negligible amount for our team considering our emphasis on the frugality of our prototype. Another option we considered was to purchase additional steel and hire a welder to weld additional pieces on the outside of the lever arm. This would allow our team to put our points of rotation on the outside of the lever arm that we had already purchased. A problem with this solution, however, was that it required all major subsystems to be redesigned to accommodate the new lever arm: something that we felt we might not have the time to do and still complete our prototype for testing.
Figure 1: Lever Arm Prototype Design Iteration. Note the change from through holes on the lever arm to outer weldments to handle the rotating bolts between the compound lever connections. Courtesy of R. Guerrero, M. Copic, K. Ellis, L. I. Marcia.
We did not want to compromise the factor of safety associated with our design nor did we want to push the cost of materials of our prototype to be over $750 USD. Moreover, we did not want to wait any longer for additional steel pieces, as our lead times for steel from online vendors was between a week to a week and a half. Because we already had our square tube ordered and still had other pieces to fabricate, our team decided upon the second option. We split the team into two halves, where one team was working in Solidworks and FEA to make the necessary design adjustments, and the other team was moving forward on parts fabrication. Had we waited on additional pieces our design may have remained relatively the same as before, but it would have meant that our team would have spent at least another $100 and wait another week and a half to get a larger steel lever arm.
Prototype Testing:
It is extremely difficult for teams to have an iterated prototype ready for testing and presentation for the Senior Design Conference. That being said, judges at the Senior Design Conference will expect your team to have quantitative as well as qualitative justifications for the validity and ingenuity of your design solution. These justifications can only come from experimental data that supports or challenges the intentions and expectations behind the design solution. This requires that your team has as complete a prototype or conceptual design representation as possible-- and with enough time to get quantitative data ready to convey to an academic audience.
What is considered “ready” for the Senior Design Conference?
Readiness is largely dependent on the nature of the design project. Project areas such as virtual reality, app design, city planning, and building design are validated through software and are either too expensive or infeasible to realize before the end of the senior design project. However, for a hardware oriented project such as my team’s project, the Frugal Clay Press for Nicaragua, “readiness” demanded that my team had a standing and fully functional prototype of the press that had been tested using proper scientific methods.
Regardless of the nature of the project, your design team is responsible for quantitatively validating your design solution through use of scientific methods of testing and data collection.“Readiness”, in the experience I have had in the senior design project, means that your team is able to have as close to a finished prototype as possible with enough time remaining to collect enough data on the safety and effectiveness of the design.
Because design validation is an important criteria for the evaluation of your senior design project, your team will need to be able to determine what amount of progress and prototype completion is acceptable for the design to be ready for testing. Utilitarian cost-benefit analysis comes into play when determining how much time should be allotted to collect adequate data on the performance of your design solution, while minimizing the chances that the prototype will not be functional or safe to operate.
Safety of Prototype Construction & Testing Procedures: As important testing may be in design validation, your team must also have completed thorough analysis of safety hazards and failure theories associated with your design before prototype construction begins. The same care must be given by your team in the design of experiments for your prototype.
When considering how safety in prototype construction and testing factors Utilitarian considerations in decision making:
- What functionalities, subassemblies, and aspects of your design solution are absolutely necessary to have completed in order for the prototype to execute its main functionalities safely? Can peripheral functionalities, subassemblies, or small aspects of your prototype be omitted to maximize the amount of time for your team to test your prototype, without compromising the safety and effectiveness of the design?
- Does your team have the time to purchase, fabricate, and/or assemble your prototype while abiding by the tolerances, factors of safety, or other safety concerns specified by your team before the Senior Design Conference? Can these tolerances be ignored to maximize the amount of time to test your prototype without compromising the safety and effectiveness of the design?
Functionality of Prototype & Quality of Prototype Completion:
Achieving the main functionality expected of prototype does not guarantee the quality of the design solution. Your team may be successful at building a solar cooker that is able to reach high enough temperatures for cooking and baking, but find that parts of the cooker melt if out in the sun for more than an hour. Addressing problems in the prototype requires redesign and iteration. Time, however, may not allow your team to iterate upon your prototype. This brings teams to maximize the amount of time spent increasing the quality and performance of the prototype through iteration, while still having time to conduct prototype tests and collect data for presentation at the Senior Design Conference.
When considering how prototype functionality and quality in prototype construction factor Utilitarian considerations in decision making:
- Define the main functionality of your design. Are there peripheral functionalities that can be omitted from the prototype to maximize the available time for your team to collect data on your prototype, without compromising the safety and effectiveness of the design during operation or testing?
- What are issues that your team finds through testing your prototype? If these do not impact the main functionality of your prototype, can these issues be safely tabled for further iteration to maximize the available time for your team to collect data on your prototype?
- Suppose your team has a design issue that has a temporary solution that will hold until the Senior Design Conference, but should not make it into the final design. Can these solutions be implemented quickly without compromising the safety and effectiveness of the design during operation or testing?
Personal Link:
My team faced a significant issue with our assembly about three weeks before the Senior Design Conference in the base fixture assembly of our clay press. There were steel members in our design that were supported by ⅛ inch thick steel L-brackets. These L-brackets were responsible for supporting the structure during clay compression. After purchasing our steel angle that we planned to use for the support brackets, however, finite element analysis (FEA) on the part indicated that using a single L-bracket in the rear would lead to breaching the implemented factor of safety of several parts of our system. Because we were already a week behind on fabrication and could not wait to order thicker brackets, our team decided to screw L-brackets on top of each other in pairs and use them as one supporting L-bracket. These L-bracket pairs were to be screwed together in our assembly until after the Senior Design Conference, when we would then weld the brackets together for a stronger supporting piece.
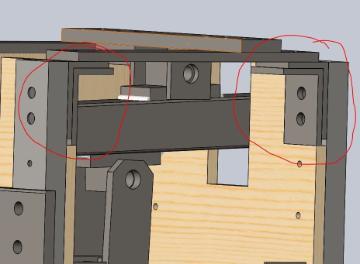
Figure 2: The implemented double L-bracket support for the Frugal Clay Press Base Fixture assembly. This was implemented solely because our team did not have the time to redesign a support or purchase additional material to make a better part. Our calculations in FEA determined failure for these pieces, but only at stresses three times that of what we expected.
We chose to implement a temporary mechanical solution to our assembly issue for two main reasons. First, we wanted to be able to have a standing prototype prepared the week prior to the Conference to allow our team to conduct clay compression tests using the prototype. These tests could then be presented to help validate our design concept and demonstrate the key functionalities of our clay press. The second main reason was that we were aiming to limit the cost of materials for our first prototype to be under $750 USD. This budget was important to ensure that our Frugal Innovation Hub project did, indeed, emphasize frugality in the design. Understanding that our project was intended to be an actual product intended for a real customer beyond the Senior Design Conference, our team chose to minimize the costs related to our initial prototype to maximize our opportunities to both iterate our prototype once more and return to Nicaragua to deploy our project in the community.